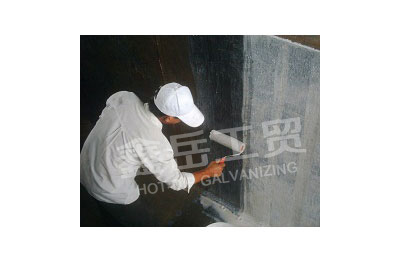
Design and Construct Hot Dip Galvanizing Plants both Domestically and Internationally
Add: Jinshan Bridge Zone, Xuzhou, Jiangsu, China
Mobile: 86-13805211808
Tel: 86-516-83168088
Email: xy-rjd@163.com
Action mechanism: The zinc pot is one of indispensable key equipment with high value and easy consumption in the hot dip galvanizing production. Because the high value and easy consumption of zinc pot decreases the economic benefit of hot dip galvanizing factories considerably, how to find a new material to insulate molten zinc from the pot is very important for hot dip galvanizing factories and also a difficult problem to be solved necessarily for many engineering and technical personnel in hot dip galvanizing field. Through the common effort of many scientific and technical personnel, our company has developed “XG-T-2 protection coating for internal wall of zinc pot”. The protection coating can effectively prevent the corrosion of zinc pot by molten zinc and decrease energy and material consumption, and so it is well received by customers.
Mechanism of action:
The composite “industrial ceramic” on metal surface is one of important methods prevent the corrosion of metal in high temperature and liquid nonferrous metal media. Its action mechanism is to insulate metal article from external media for preventing the corrosion of metal surface by external media and liquor.
Composite “industrial ceramic” coating should satisfy the following basic requirements: (1) compact, integrated and impervious structure without pore; (2) strong bond force with base metal; (3) high hardness, wear resistance and corrosion resistance; (4) uniform distribution on whole protected surface and good hot consistency with base body; (5) able to overcome hot deformation caused by different expansion coefficient of two materials.
Using method:
Stir liquid coating and make it uniform during construction, directly apply coating on the internal wall of zinc pot whose rust has been removed, after self-dry state apply coating again to it, the time for two applying is controlled within 3 h, total thickness is 0.1 mm, natural dryness at room temperature for 24 h ( it would be best if dry time could be 48h), after dryness sintering and solidification are conducted according to heating up curve (sintering, solidification, baking and zinc smelting can be carried out, but when zinc is added do not bump the coating )
Temperature curve figure of sintering and solidification